underspecified electrolytic capacitors,
a new paradigm in electronic planned obsolescence
a rant by ralph klimek
2-jun-2009
keywords: bulging electrolytic capacitors, ESR, equivalent series resistance,rant
This
rant's subject concerns the usage of electrolytic capacitors in power
supply smoothing applications to enforce planned obsolescence
strategies in both professional and consumer grade electronic equipment.
The
subject matter of today's rant was inspired by the slowly
degrading performance of equipment that I maintain at work. The
equipment is supplied by a leading manufacturer of networking
equipment. I have no quarrel with the vendor, they have done the utmost
to help us and will accept and replace damaged equipment without
arguement. I think they are the innocent party in this problem, so I
have taken pains to ensure that they cannot be identified by my rant. I
have also replaced a number of damaged capacitors on expensive computer
PC motherboards , restoring lost reliability.
However, I decided
to mount my soapbox when I found this very nice PC ATX power supply in
the dumpster. It appeared to be almost new, it was the advanced
atx model with sata connectors and the new wide atx motherboard
connector, a desirable item. What was it doing in the rubbish ?
Knowing from past experience that good things are discarded . not for
lack of function, but because they are no longer bright and shiny.
I took it home and put it on my dummy load. It powered up
for a few seconds and then crowbarred, ie, the overvoltage alarm had
tripped and shut down the primary inverter. This power supply was
effectively dead, but not irreversibly so. At least not to me.
There
were no obvious signs of burnt out components and a quick multimeter
pass revealed that the inverter transistors, fuses, diode et al
were good. I then noted one peculiar thing. There
seemed to be very few electrolytic capacitors on the low voltage
output side. Good design practice dictates that the 5V rail
have not merely one but 5 or 6 capacitors in parralel. The reason for
using so many is because of the high current spikes that are coming
out of the step down transformer and shcotky rectifiers are of
many tens of amperes of peak current. Your logic circuits dont
want this kind of rubbish, they prefer nice clean DC please. Real
electrolytic capacitors have a parasitic resistance that is frequency
dependant, electrode geometry dependant and electrolyte dependant. This
parasitic resistance is real, and, being real, really turns amps into
watts! These high current pulses heat these devices. You
put many capacitors in parallel to spread the quite onerous burden of
sinking these multi ampere pulses.
Electrolytic capacitors are sold with two primary specifications, maximum sustained working voltage, and capacitance.
There
are other specifications, sometimes published by the vendor, usually
not, and that is equivalent series resistance, (ESR). For simple
smoothing applications , for example, linear PSUs (plugpacks et
al), audio frequency coupling and decoupling, electrolytic caps
can have moderate to high ESR and work perfectly fine for
these applications and have an arbitrarily long life if their voltage
rating is respected. This life can be thirty years or more. I
have seen fifty years life in some pioneering equipment.
Modern
switch mode power supplies with their extreme pulse currents demand low
ESR devices. These first become available about 30 years ago with the
first generation of switchmode regulators. The equivalent series
resistance is never indicated on the device itself, unlike the voltage
and capacitance rating. It is only ever specified in the manufacturers
data sheets...if available.
Like
all electronic
components, the power dissipated, temperature and lifetime relationship
is well characterized and governed by some simple rules of thumb,
allowed for by statistical analysis. The general rule of thumb is
that for every 10 degree C increase in operating temperature, the
average lifetime of an commercial electronic component is halved.
Devices supplied for defense or advanced commercial needs are
very tightly specified with temperature derating curves and accelerated
aging testing that can reliably predict device lifetimes given a
service temperature and operating condition. Are you smelling a
rat here ? Put on your tin-foil hat. I recenly acquired a
capacitance meter that could measure electrolytics precisely, by timing
how long a charge took at constant current. It revealled the
obvious. A ruptured electrolytic has lost over 99 percent of its rated
capacitance. One that had merely bulged, but not actually
ruptured, had lost anywhere between 50 to 90 percent of its rated
capacitance.
I
have recently come to the conclusion that the cause of the "bulging" is
due to the absence of one key stabilizer in proprietary electrolytes. I
believe ( without proof ) that the missing ingredient is a gas
recombination catalyst. The gas is hydrogen and oxygen from simple
leakage current induced electrolysis. That catalyst is most
likely a trace of platinum or palladium. That alone is sufficient
economic reason to exclude it !
The conditions under which
"low ESR" devices must labor are onerous. The thermal conditions
inside the average consumer PC PSU are particularly onerous. The
pathetic excuse of a cooling fan serves only to exhaust pre-heated air
from the PC enclosure to the outside. You cant cool
something with hot air, unless your thing that you are trying to cool
is hotter already! Power electronics must be kept cool, this is not
news. An electrolytic capacitor is particularly vulnerable to
over temperature conditions especially in switchmode smoothing
applications.
some theory
The capacitance is a measure
of how much charge an object can store. It is a strong function of
geometry and material properties. The capacitance is inversely
proportional to the seperation of the electrodes. In the real world,
electrodes are seperated by air, oil, paper, assorted polymers. Such
capacitors do not have the capacitance required to perform the SMPS
smoothing
function. However, what if the seperator was an molecular
thickness of an impermiable substance...say aluminium oxide ? It
has a very high band gap, is mechnically strong, it adheres to a
metallic aluminium substrate with great tenacity. It is easy to form
and better still it is cheap!
An aluminium electrolytic
capacitor was invented in the 1920s, its nothing new. There are
two metal foil electrodes, a mecanical sepparrator , ususally paper or
now advnaced polymer mesh and a water based electrolyte, usually based
on ammonium borate and proprietary stabilizers. The electrodes
and seperator is rolled up into a cylinder, canned with electrolyte
solution and then hermetically sealed. The actual insulator is a
molecular film of aluminum oxide which is grown be electrochemical
action after the first "forming charge" is applied. One electrode
of the capacitor is the metal with oxide film, the other electrode is
the metal, it is the conductive electrolyte. The "plates" of the
capacitor being only a couple of molecules thick, and being so close to
each other, the geometry of the device now acquires a very high
capacitance and large amounts of charge can be stored at moderate
voltage.
The ESR of such a device is governed by the specific
molar conductivity of the electrolyte and the thickness of the metal
foil in the electrodes. A low ESR device is necessarily larger.
A high temperature and high voltage will lead to electrolysis of
the electrolyte and the inevitable generation of gas when the water is
broken down into its hydrogen and oxygen. A good capacitor may even
have a catalyst to recombine the gases. (that is speculation on my part)
Many
of you reading this may now be going "ah-ha!" . You will have
come across the recent phenomena of the "bulging capacitor". The
modern cap has inbiult fracture lines stamped into the little metal
can. When internal gas pressure is extreme, the can will gently rupture
and expell their contents. They used to detonate! When a capacitor
ruptures it irreversibly looses the electrolyte that is essential to
its operation. Its capacitance goes down and its ESR goes up, thus
dissipating even more power and getting hotter and hotter. The DC
that it is trying to smooth becomes noisier and riddled with
transients. Your equipment becomes intermittant, behaves like its got
gremlins, your pooter keeps blue screening untill it just stops
working. Is this familiar....anyone ? Open up your power supply
and have a look. Examine your computer motherboard. If you are
getting aberant behaviour it could be due to bulging caps. They can be
replaced, any competant electronic hobbyist is capable of doing so.
for the tin-foil hatted or the bright-young-things-with-harvard-mba
conspiracy theory one
Equipment lifetimes can be controlled by carefull selection of switch mode regulator smoothing capacitors.
conspiracy theory two
This has already happened
images of damaged equipment
 |  |  |
 | this
otherwise well made network gear had become erratic and intermittent as
a result of noisy power rails caused by these damaged capacitors | 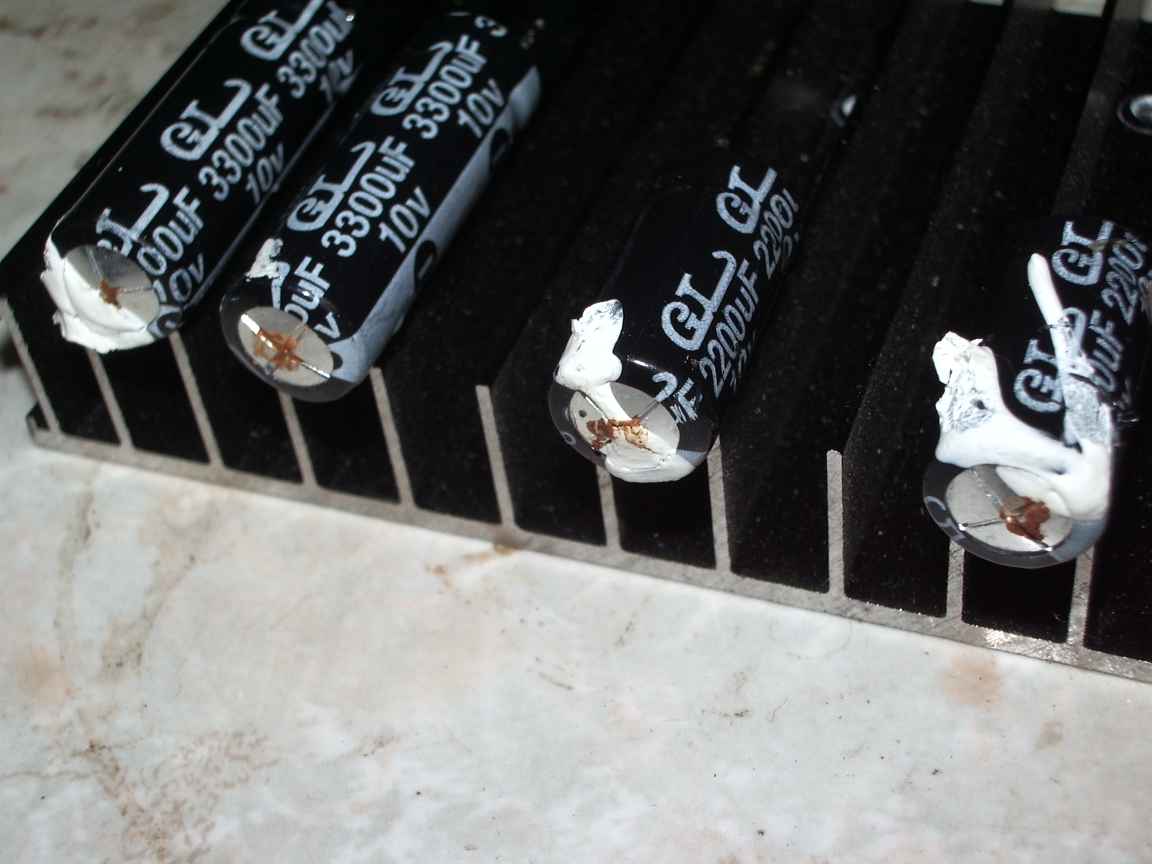 |
| | damaged caps from this PC PSU these have ruptured and expelled their contents |
 |  |  |
damaged caps from PC PSU. The measured capacitance was only 150uF instead of 3300uF | after my repairs | after my repairs close-up |
 | The
real question is why were there so few output smoothing caps in this
PSU. No doubt the ESR and capacitance rating was in spec when this was
assembled but it clearly did not stay working for very long. My
replacements came from the junkbox. For completeness and piece of
mind, I will be making an outboard PCB containing extra paralled
capacitors to ensure that the PC will have clean 5V and 12V rails |  |
otherwise a really nice, expensive PSU | | otherwise a really nice, expensive PSU |
Ha
! Thats nothing. I have recently recovered some nice lcd flatscreen
monitors that were discarded because they were none functional.
The
business part, the lcd flat screen had in all cases been carefully and
well constructed by the Japanese and Taiwanese flat screen businesses
that do this sort of thing very well. However, the power supplies had
been made by the cheapest contractor that could be found on the day.
The problem and solution should come as no surprise. These
otherwise perfectly good lcd screens were dead because of bulging
electrolytics in the rubbishy power supplies. Replacing
these has now brought an embarrassing over-abundance of good flat
screen monitors. Gosh this world is weird. Here is another
tip. If you find a discarded monitor in the dump that uses an external
power brick, the usual reason for discarding the monitor is that the
previous owner has lost the power brick, experience has shown that that is allmost never anything wrong with the flat screen.
 |  |
rear of a Mitsubishi 17 inch lcd monitor the psu board is made by Benq | replacing these 3 bulging caps got it going |
copyright declaration: none, this article is copyleft, quote it, copy it, use it as you see fit

mod record page created Tue Jun 2 19:17:04 EST 2009
added flat-screen monitor image
it was a dark and stormy night...